With its efficient and flexible processing advantages, laser cutting machines have been widely used in all walks of life. Lasers were first used for cutting back in the 1970s. In modern industrial production, laser cutting is widely used in sheet metal, plastic, glass, ceramic, semiconductor, textile, wood and paper processing. In the next few years, the application of laser cutting in precision machining and micromachining will also grow substantially.
In 1917, Einstein proposed the theory of "stimulated emission", and Maiman announced in 1960 that he had obtained the first laser beam in human history. Laser is called Laser in Hong Kong, Macau and Taiwan, from the transliteration of its English word Laser. According to the principle of laser generation, in 1964, the famous Chinese scientist Qian Xuesen officially changed his name to "laser".
A laser is a type of light, like electroluminescence in nature, which is caused by changes and spontaneous emission of atoms (molecules or ion kites). Although the laser is light, it is significantly different from ordinary light. The laser only relies on spontaneous emission for a very short period of time at first, and the subsequent process is completely determined by the stimulating radiation, so the laser color is very pure, there is almost no divergence direction, and the luminous intensity is very high. Laser has four characteristics: directional light, high brightness, pure color, high energy, also known as "the fastest knife", "the most accurate ruler", "the brightest light".
Laser has the characteristics of high correlation, high intensity, and high directionality. After the laser generates laser light, the laser light is transmitted by the mirror and irradiated on the processed object through the collecting mirror, so that the processed object (surface) is subjected to strong thermal energy, and the temperature rises sharply.
.jpg)
What is laser cutting?
Laser cutting is to replace mechanical tools with invisible lasers, with high precision, fast cutting, not limited to cutting patterns, automatic typesetting of materials, smooth incisions, low processing costs, and green and pollution-free. Let us understand in detail how laser cutting works.
Laser cutting is achieved by using the high power density energy generated by the laser focusing. Under the control of the computer, the laser outputs a controlled repetitive high-frequency pulsed laser through pulse discharge, forming a beam with a certain frequency and a certain pulse width. Fine, high-energy-density specks, focal point near the surface to be machined, instantly melt or vaporize the machined material at high temperatures.
Each high-energy laser pulse immediately sputters a small hole in the surface of the object. Under the control of the computer, the laser processing head and the processing material continuously move relative to each other according to the pre-drawn graphics, so that the object is processed into the required shape.
Laser cutting machines focus a laser on the material, heat the material locally until it exceeds the melting point, and then blow away the molten metal with coaxial high-pressure gas or the pressure of the resulting metal vapor. As the beam moves relatively linearly with the material, the holes continuously form very narrow width seams.
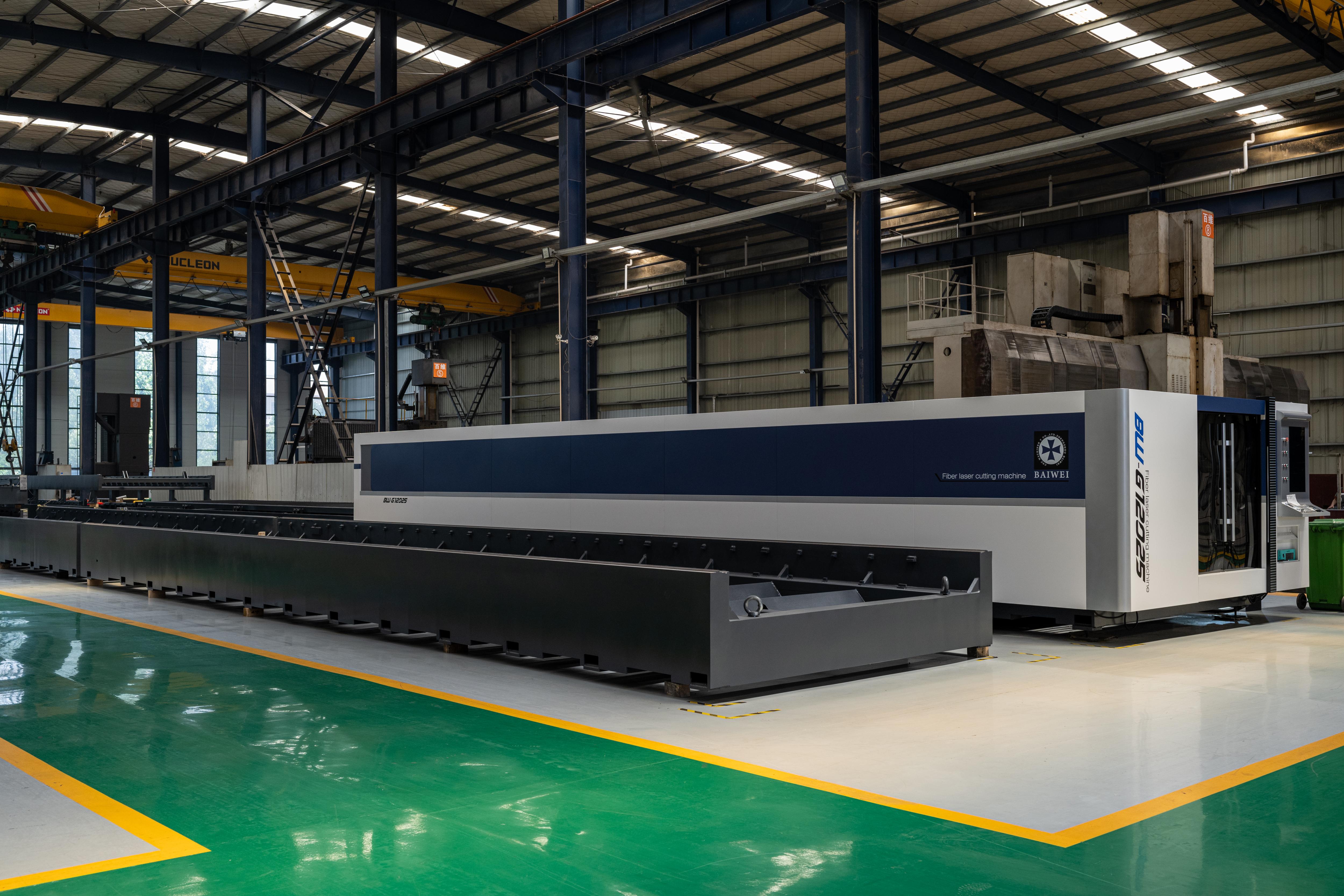
The energy released when the laser beam hits the surface of the metal sheet melts the sheet and is blown away by the gas. Laser sources typically use fiber laser beams. By means of lenses and mirrors, the laser beam is concentrated in a small area. The high concentration of energy causes rapid local heating, causing the metal plate to dissolve.
In addition, because the laser emission energy is very concentrated, only a small amount of heat is transferred to the rest of the metal plate, so there is little deformation of the material. Lasers can also cut complex-shaped blanks very accurately and require no further processing.