Laser cutting carbon steel plate belongs to thermal cutting. Under normal cutting conditions, the
cutting effect of carbon steel should be burr-free and consistent with the traction line. However, due to some improper operation and debugging, the following problems may occur, which can be adjusted according to the reasons.
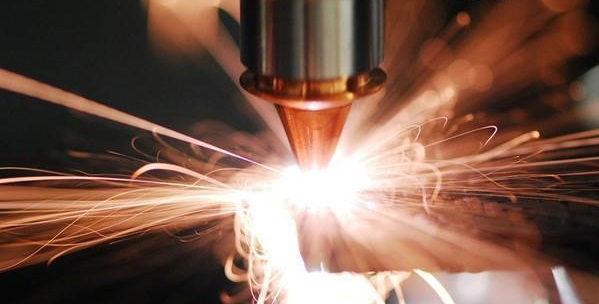
1. The pull wire at the bottom has a large offset and the cutout at the bottom is wider
Possible reasons: (1) The feed rate is too high (2) The laser power is too low (3) The air pressure is too low (4) The focus is too high
Solution: (1) reduce the feed rate (2) increase the laser power (3) increase the air pressure (4) reduce the focus
2. The burrs on the bottom surface are like slag, dripping and easy to remove
Possible reasons: (1) The feed rate is too high (2) The air pressure is too low (3) The focus is too high
Solution: (1) reduce the feed rate (2) increase the air pressure (3) reduce the focus
3. Metal burrs connected together can be removed as one piece
Possible cause: The focus is too high
Workaround: Lower the focus
4. The metal burrs on the bottom surface are difficult to remove
Possible reasons: (1) The feed rate is too high (2) The air pressure is too low (3) The gas is impure (4) The focus is too high
Solution: (1) reduce feed rate (2) increase air pressure (3) use purer gas (4) lower focus
5. There are only burrs on one side of the sheet cut
Possible reasons: (1) Incorrect nozzle alignment (2) Defective nozzle opening
Solution: (1) Center the nozzle (2) Change the nozzle
6. Material is discharged from above
Possible reasons: (1) The power is too low (2) The feed rate is too high
Solution: Press the pause button immediately when this happens to prevent slag from splashing on the focusing lens. Then increase the power and decrease the feed rate.
7. The workpiece is not cut through
Possible reasons: (1) wrong processing gas (N2) (2) feed rate is too high (3) power is too low
Solution: (1) Press the pause button immediately when this happens to prevent the slag from splashing on the focusing mirror (2) Use oxygen as the processing gas (3) Reduce the feed rate and increase the power
8. The cut surface is not precise
Possible reasons: (1) The air pressure is too high (2) The nozzle is damaged (3) The diameter of the nozzle is too large (4) The material is not good
Solution: (1) reduce the air pressure (2) replace the nozzle (3) install a suitable nozzle (4) use a material with a smooth and uniform surface
9. No burrs, the pull line is inclined, the cut becomes narrower at the bottom
Possible cause: The feed rate is too high
Solution: Decrease the feed rate
10. The cutting surface texture is very rough
Possible reasons: (1) The focus is too high (2) The air pressure is too high (3) The feed rate is too low (4) The material is too hot
Solution: (1) lower focus (2) reduce air pressure (3) increase feed rate (4) cool material
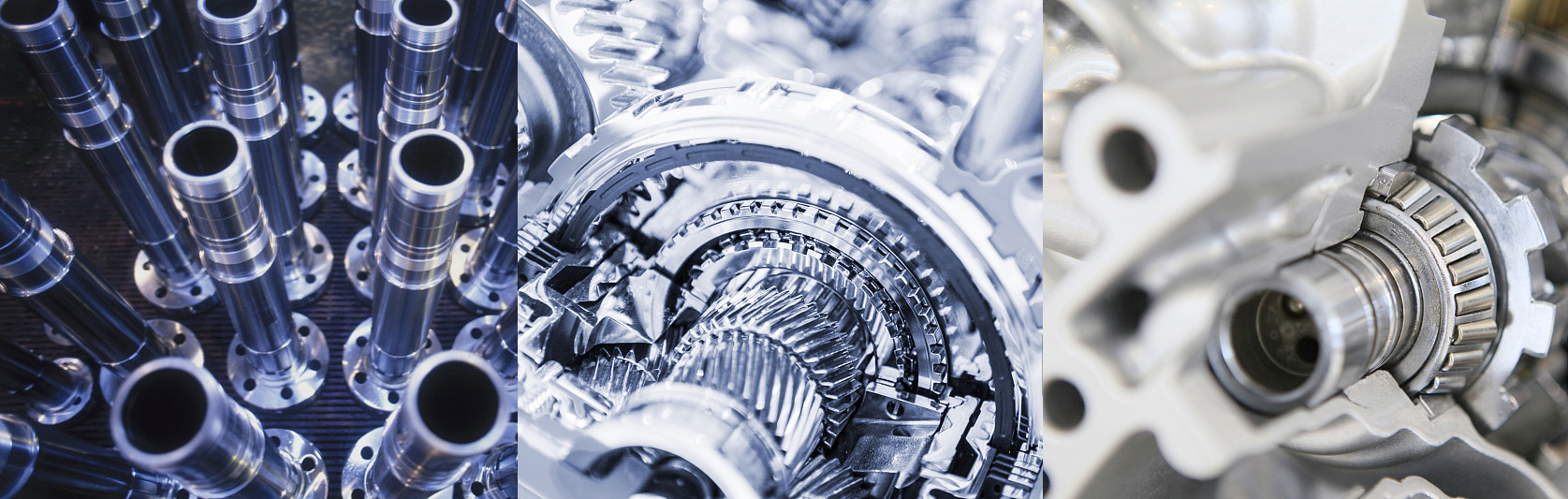